Kunststoff Druckverfahren
Aktuell gibt es eine Vielzahl von Kunststoff Druckverfahren. Diese werden wie folgt nach Technologien aufgeschlüsselt:
FDM-Druck
Der Standard unter den 3D-Druckern und wurde von Stratasys entwickelt. FDM steht für Fused Deposition Modeling (auch bekannt als FFF) und kann am Ehesten mit “Modellierung durch Ablagerung von Geschmolzenem” ins Deutsche übersetzt werden. Diese etwas sperrige Übersetzung erklärt aber auch schon recht gut das Vorgehen beim Druck.
Dabei wird der Druckrohstoff, meist Kunststoffe oder Kunstharze, die leicht schmelzen, erhitzt und geschmolzen, in den meisten Fällen wird er nur sehr knapp über seinen Schmelzpunkt erhitzt, um ihn nicht zu verbrennen, und dann wie mit einer Heißklebepistole als Faden an den jeweiligen Ort “gespritzt”. Es wird meist mit möglichst dünnen Fäden gearbeitet (0,1 -0,3 mm), die aus der Düse des Druckers, auch genannt den Druckkopf, kommen und aus denen der zu druckende Gegenstand aufgebaut wird. Das ganze geschieht meist Schicht für Schicht, so dass der Druckkopf nur in zwei Achsen bewegt werden muss, während sich die Basisplatte, auch Druckbett genannt, auf der der zu druckende Gegenstand langsam wächst, Schicht für Schicht absenkt. Die hergestellten Objekte sind schwer umformbar und sehr stabil, leider aber auch nicht sehr belastbar.
Stereolithografie
Das Stereolithografie-Verfahren ist der Klassiker und ist das bisher am längsten genutzte 3D-Druck-Verfahren, wodurch auf die größten Erfahrungswerte aufgebaut werden kann, somit der Urahn aller 3D-Druck-Verfahren und wurde von Chuck Hull bereits im Jahr 1983 entwickelt. Chuck Hull gründete später 3D Systems, einen der weltgrößten Hersteller von 3D-Druck-Anlagen. Das Prinzip ist einfach oder besser gesagt einfach genial. In einem Becken befindet sich ein flüssiger Kunststoff, ein Kunst- oder Epoxidharz. Es ist ein lichtaushärtender Kunststoff. Der Fachbegriff für diese Kunststoffe lautet Photopolymere. Das Bauteil besteht aus den Basismonomeren des zu verarbeitenden lichtempfindlichen Kunststoffs. Um einige Millimeter wird nach jedem Arbeitsschritt das Bauteil in das flüssige Kunststoffbad abgesenkt und im Anschluss daran in eine Position zurückgefahren, welche um genau den Betrag einer Schichtstärke unter der Schichtstärke davor liegt. Mit dem Stereolithografie-Verfahren ist es möglich, sehr filigrane Strukturen und glatte Oberflächen zu erzeugen, da wenig Mechanik bewegt werden muss. SLA ist als ein äußerst präzises Verfahren bekannt. Um für Sie ein Objekt im Stereolithografie-Verfahren herzustellen, brauchen wir von Ihnen als Grundlage das dreidimensionale CAD-Modell.
Unter Stereolithografie gibt es jedoch unterschiedliche Möglichkeiten den Kunststoff auszuhärten. Die eine Möglichkeit ist die bereits oben erwähnte Aushärtung durch einen UV-Laser, auch genannt SLA-Verfahren.
Eine andere Variante ist das Aushärten durch Licht, das Digital Light Processing, kurz DLP-Verfahren. Es wird ein Projektor verwendet, um Photopolymer-Harze zu erhärten. Die DLP-Technologie ähnelt SLA sehr, mit dem Unterschied, dass anstatt eines UV-Lasers eine Dunkelkammerleuchte zum Erhärten des Photopolymerharzes benutzt wird. Es ist schneller als das SLA-Verfahren, da die komplette Schicht gleichzeitig ausgehärtet werden kann.
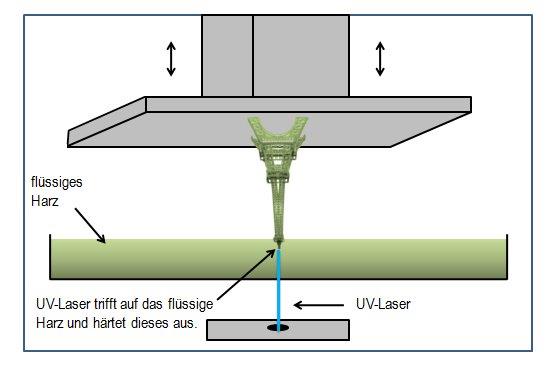
Copyright: http://printit-3d.de/unser-service/sla/
Pulverdruckverfahren
Beim Pulverdruckverfahren, kurz mit 3DP abgekürzt, wird mit pulvrigen Druck-Grundstoffen gearbeitet. Es wird hauptsächlich mit Gips oder Kunststoffpulver gedruckt, aber auch Keramik, Glas und andere pulverförmige Materialien können verarbeitet werden. Der am häufigsten verwendete Kunststoff ist Nylon12. Durch gezieltes Erhitzen wird der gewünschte Gegenstand erzeugt. Auch hier wird wieder Schicht für Schicht von unten nach oben gearbeitet. Jedes Mal wird dabei die Basis abgesenkt und eine neue Schicht Pulver auf der gesamten Fläche aufgetragen. Ein oder mehrere Druckköpfe tragen auf die Schicht einen flüssigen Klebstoff als Bindemittel auf. Das Pulver härtet an diesen Stellen aus. Das funktioniert streifenweise, in etwa wie bei einem normalen Tintenstrahldrucker. Der oder die Druckköpfe zeichnen ein 2D-Bild einer jeden Schicht auf das Pulverbett und verkleben die Materialpartikel. Der Kleber wird dabei so dosiert, dass sich auch die übereinanderliegenden Schichten untereinander verkleben. Dadurch entsteht der Gegenstand als 3D Gebilde in einem soliden Würfel aus Pulver. Das restliche Pulver muss im Nachhinein entfernt werden (mit Pinsel, Staubsauger, Gebläse etc.).
Stützmaterial ist bei diesem Verfahren nicht erforderlich. Das nicht verklebte Pulver dient als Auflage für die neue Pulverschicht ist damit automatisch Stützmaterial für Übergänge und Hohlräume. Das nicht verklebte Pulver kann durch Abklopfen oder mit einer Pressluftpistole entfernt werden. Das dabei zurückgewonnene Pulver kann für den nächsten Druck wiederverwendet werden. Eventuell sollte man es vorher sieben.
Meist müssen die Modelle nachbearbeitet werden. Durch Eintauchen in Harz dringt dieses ein, verfestigt das Material und schützt vor Feuchtigkeit. Die Modelle sind allerdings nicht sehr bruchsicher, da das verklebte Pulver sehr spröde ist. Die Auflösung hängt von der Feinheit des verwendeten Pulvers ab.
Ein weiterer entscheidender Vorteil dieses Verfahrens ist, dass mit farbigen Klebern und mehreren Druckköpfen auch farbige Objekte gedruckt werden können. Eine Anwendung »just for fun« ist das Drucken gescannter Personen in Echtfarben. Aber dafür sind die Geräte in den meisten Fällen zu teuer.
Das Verfahren wurde 1993 am Massachusetts Institute of Technology (MIT) entwickelt und patentiert. Der Pionier dieser Technologie, die Firma Zcorp, brachte kurz danach Seriengeräte mit diesem Verfahren auf den Markt, die ZPrinter. Zcorp wurde 2012 von 3D Systems übernommen, die diese Geräte weiterhin bauen und in die ProJet-Produktreihe integriert haben.
Filament Metal Printing
Zuerst wird ein geeignetes Bindersystem sowie ein passendes Metallpulver ausgewählt. Danach wird aus dem Binder und dem Metall ein Feedstock, vergleichbar mit einem Kunststoffgranulat, hergestellt. Aus dem Feedstock wird im nächsten Schritt ein Filament produziert, das wie ein normales Kunststofffilament im EVO-lizer 3D Drucker verarbeitet wird. Hier muss unbedingt darauf geachtet werden, dass der Innenraum beheizt ist und gehärtete Düsen eingesetzt werden. Nach dem Druck erhält man das sogenannte Grünteil, welches ab diesem Schritt gleich wie ein MIM oder PIM Grünling behandelt werden kann. Beim Entbindern wird der Großteil des Binderpolymers entfernt. Hierbei gibt es verschiedene Binderverfahren. Wie zum Beispiel thermisches Entbindern , kathalytisches Entbinder oder auch Lösungsmittelentbindern. Nach dem Endbindern erhält man das sogenannte Braunteil. Dieses ist nun sehr brüchig und besteht fast nur noch aus Metallpulver welches über sehr wenig Restpolymer (Backbone) zusammengehalten wird. Im letzten Schritt wird das Bauteil nun bei über 1300°C gesintert. Hierbei schrumpft das Bauteil je nach Feedstockrezeptur um bis zu 20%. Nach dem Sintern erhält man ein fertiges Bauteil aus reinem gesinterten Metall. Jegliche Kunststoffreste wurden während des Sinterprozesses verbrannt.
SLS-Verfahren
Das Prinzip des selektiven Lasersinterns, abgekürzt SLS-Verfahren, ähnelt wiederum dem des Pulverdruckes. Hier wird allerdings ein Metallpulver schichtweise aufgetragen, das danach mit einem Hochleistungslaser (CO2-Laser) unter einer Schutzatmosphäre verschmolzen wird. Dadurch backt das Material zusammen, und auch die einzelnen Schichten verschmelzen miteinander. Der Laserstrahl wird wie beim SLA-Verfahren zeitweise über das Druckbett geführt. Das erfolgt auch hier über ein Umlenksystem mit beweglichen Spiegeln. Jedoch hat dieser Druck königliche Preise. Stützmaterial ist wie bei allen Pulverdruckverfahren nicht notwendig, da das nicht gesinterte Material als Auflage dient. Anwendungen findet das Verfahren bei der Produktion von Kleinserien für Flugzeugbau, Dentaltechnik sowie bei der Verarbeitung von Keramikmaterial und Glas.
PolyJet- bzw. MultiJet-Verfahren
Beim PolyJet-Verfahren, auch MultiJet Modeling genannt, kurz MJM, wird ein lichtaushärtendes Polymer durch einen Druckkopf mit mehreren Düsen auf eine Werkplattform aufgetragen. Das noch flüssige Material wird durch UV-Licht sofort ausgehärtet. Danach fährt die Plattform um die Dicke einer Schicht nach unten. Die Schichtdicke beträgt je nach Maschine zwischen 16 – 32 µm. Anschließend wird eine weitere Schicht auf die bereits ausgehärtete Schicht aufgetragen. Dieser Prozess wird so lange wiederholt, bis das Modell vollständig gedruckt wurde. Dadurch, dass das Material in Tropfen durch die Düsen aufgetragen wird, zerläuft es vor dem Härtungsvorgang. Somit sind mit bloßem Auge, nahezu keine Rillen im Werkstück zu erkennen und die Oberfläche ist sehr glatt.
Der Polyjet-Drucker besitzt mehrere Druckköpfe. Der große Vorteil besteht darin, dass mit verschiedenen Materialien oder auch in verschiedenen Farben gedruckt werden kann. Falls das Modell überhängende Bestandteile hat, werden diese mittels Supportstrukturen abgestützt. Diese Supportstrukturen oder auch Stützkonstruktionen müssen nach der Fertigung entfernt werden.